What is active supervision?
As opposed to passive supervision, active supervision is a management strategy that involves reaching out to information and people to anticipate problems and performance issues in order to proactively drive performance.
To achieve this, managers must take action, among other things, by conducting field trips, also known as active supervision tours or Gemba walks.
Examples of active supervision activities:
-
Assigning employees to their workstations
-
Basic checks (quality, customer specifications)
-
Volume / time tracking
-
Active supervision tour / Gemba Walk
-
Monitoring of all performance parameters (productivity, quality, health and safety, etc.)
-
Capture of performance gaps
-
Communication of performance gaps
-
Proactive management (anticipate, use checklists in the field...)
-
Continuous improvement
How can you manage proactively?
Here are 7 useful tips:
- Inventory strategic checkpoints
- Define a checkpoint validation framework
- Align team time management with objectives
- Engage in active supervision on a daily basis
- Include at least 30% prevention in the workload
- Thoroughly plan your schedule
- Measure the proactive management actually carried out
We’ll get more into these in a bit, but first, let’s rewind and get some perspective on proactive management.
The light bulb series analogy
Imagine having to change a light bulb in your house. Not rocket science, you might say. Now imagine that your house has over 500 light bulbs connected in series and that these break randomly throughout the day. If you're the only one changing the bulbs, your chances of spending the day in the dark are high!
Prevention: from the 60s to today
This scenario is very unlikely, you may say. However, in the early 1960s, maintenance reliability was limited to replacing a component only when it failed. This practice created a vicious circle in which the more breakdowns there were, the more delays there were in deliveries, and the more production time had to be increased to compensate for the uncertainties and risk management. It goes without saying that this business strategy and the chain reaction it created directly impacted production costs, resulting in reduced profits.
In an economy where globalization has brought a competitive dimension to a level never seen before, the gymnastics of operations management was given a new twist when the concept of preventive maintenance was finally introduced. The simple (but brilliant) idea of scheduling recurring maintenance activities to prevent failures rather than react to them resulted in a reduction of total unplanned downtime, thereby reducing the trend of rising costs and, more importantly, regaining control of operations.
How to adopt proactive management?
Based on the preventive maintenance model, we must think about the "lightbulbs" that are most likely to cause us problems (or that have historically caused us problems) and adapt our inspection frequency accordingly.
The proactive manager's role involves a number of recurring activities on a schedule and checkpoints to avoid an unexpected event. If less than 30% of your day is dedicated to supervision, follow-ups or coaching, the chances are that your "maintenance plan" is insufficient for reducing the proportion of emergencies in your everyday schedule ad that you’ll need more contingency plans to deal with it.
Here are a few simple and easy-to-practice tips that can greatly improve your management style and help you become a proactive leader that stays away from the old reactive approach.
1. Inventory strategic checkpoints
Make an inventory of the checkpoints that impact the strategic objectives for which you are responsible. If you realize that certain checkpoints are missing, consider adding them to your routine.
2. Define a checkpoint validation framework
Determine who is responsible for these checkpoints. If you are not responsible, make sure you clarify your expectations with the person concerned :
-
What's the validation method for these checkpoints?
-
What's the expected result?
-
To meet our objectives, what agenda is most appropriate?
3. Align team time management with objectives
Take the time to validate whether your team's time management is aligned with these goals, and identify "time-consuming" elements to eliminate from the team’s daily routine.
4. Engage in active supervision on a daily basis
Develop the habit of "seeing for yourself", a technique also known as Gemba Walk, related to the Japanese concept of Genchi Genbutsu to avoid a gap between your expectations and the perception of others.
5. Include at least 30% prevention in the workload
Organize your schedule so that at least 30% of your time is invested in prevention rather than cure.
For example: 1-on-1 coaching, frequent follow-up meetings, time spent communicating your vision, taking the pulse of team morale, etc.
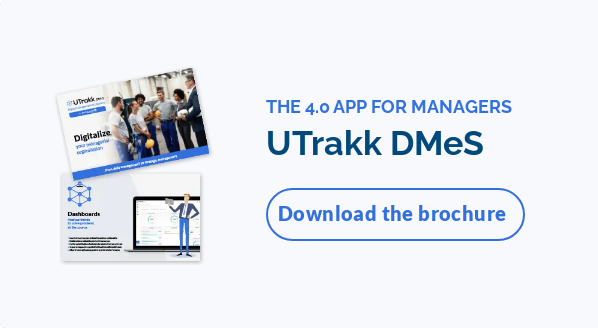
6. Thoroughly plan your schedule
Plan, plan, plan. The more time you spend planning your schedule, the easier it will be to assess an opportunity cost in the event of an emergency; instead of dealing with it, you will ask yourself: "Is this emergency more important than what was already on my schedule? "
7. Measure the proactive management actually carried out
Take stock of yourself! Take a step back to assess the achievement of your "ideal week" on a regular basis and analyze the sources of discrepancies in order to address them.
Of course, emergencies will always be part of our daily lives and it is impossible to avoid them all. However, they should not take up the majority of our time, and this is the most important thing to remember about this philosophy.